Design and Analysis
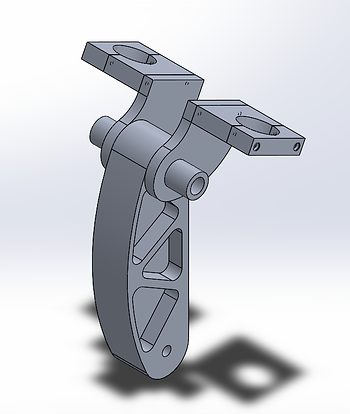
Approach
There are a few different methods to be considered when going about making the MX SnowSki components. The material and machines that will be used to produce these parts are important and must be utilized correctly to ensure the lowest costs. The spindle is structurally the most important piece to this project, since it controls where all the other components placements and orientations are, relative to the pre-existing forks. The spindle also has a few different designs to be considered. The spindle could consist of two or more machined pieces that would either be bolted or welded together, as well as the possibility of being one large machined piece. For time and material constraints we will probably use a few machined parts to keep from purchasing one large block of 6061 and shaving a lot of unused material off. This will then be bolted to a mounting bracket of 6061 aluminum, which is attached to the SnowSki. The top part of the spindle needs to be bracketed to the forks to keep rotation from occurring as well as housing the stock front axle to keep the assembly in position and good functionality. The SnowSki will be bought, but will need to work and fit properly with our designed components.
Benchmark
A company based out of Idaho makes a similar product called the Timbersled Mountain Horse, which consists of a large track, suspension, and gear combo for the back of a dirt bike for its main source of propulsion through snow and ice. This rear assembly for the Mountain Horse costs about $5,300 and is why we will be utilizing a paddle tire in place of the rear wheel. This company also makes a front ski assembly, which is called the Timbersled BackCountry Ski. This ski assembly is well made and optimizes the need for stability and strength in the front of the snow bike. Our design will be similar in regards to function but will optimize the weight and ski stability as well as making the final product look aesthetically pleasing.

Parts were designed for proper fitment on a 2005 CR250 MX bike, as well as being optimized for a low overall weight. The calculated parameters of each part mainly considered the optimization of weight, but are also focused towards keeping raw materials smaller to help keep the cost of the project down. Most dimensions were chosen for proper fitment on the MX bike, but were scaled down on thicknesses of materials or hardware to optimize the cost of the project. Each component was analyzed with safety in mind.
Calculated Parameters
The prediction for our device is that the ski and spindle shall be able to support a 500lb load (A-Pg. 5) without buckling or failing. The device will also keep from rotating about the front wheel axle, since the brackets will snugly fit to the front forks and hold the spindle in place. The front ski shall be able to rotate 20-45° in an incline past horizontal equilibrium as well as 15-30° in decline. The front ski will handle tight and wide sweeping turns in snow without the device failing/breaking.
Performance Prediction
This project was designed with the intention of being built at CWU with the available resources in the machining and materials labs. The work for the project will be within the constraints of the technology available by using the appropriate machines when needed, such as machine lathes, mills, CNC’s, and drill presses. The technology available to us was a limiting factor for this project since the ski was originally going to be designed, built, and tested as well. Unfortunately, the injection-mold machine wouldn’t produce the correct geometry of the part, since the ski would be quite large.
Methods and Construction
![]() 20150220_114929_edited.jpg | ![]() 20150222_180948_edited.jpg |
---|---|
![]() 20150222_180929.jpg | ![]() 20150222_181052_edited.jpg |
![]() 20150302_163213_edited.jpg | ![]() 20150227_125434.jpg |
![]() 20150302_163203.jpg | ![]() 20150302_163246.jpg |
![]() 20150302_163252.jpg | ![]() 20150309_103528.jpg |
![]() 20150227_115456.jpg | ![]() 20150220_114936.jpg |
![]() 20150302_163238_edited.jpg |
Testing Method
The testing portion of the project would take into account the requirements set earlier in the report. These requirements included: that the total weight of assembly would be ≤ 10 lbs, the ski should rotate 20-45° to its incline and 15-30° to its decline, the spindle shall not rotate > 2° when installed on forks, and the column must be able to support a 500 lb load.
The main parameters of interest are the angles achieved by the ski, the angle of the spindle when installed on the bike, and if the column is able to support a 500 lb load. The reason that the total weight of the assembly is not as important is because it does not impact the function of the ski during the test ride portion.
Unfortunately, the ski will mostly likely not see snow for testing. It will be tested at sand dunes that are near Ellensburg, WA, which will be available through public access or certified with the use of a discover pass. Predictions for the ski’s performance are hard to gauge, since it won’t be tested on its intended surface. The kinetic/sliding coefficient of friction for plastic on snow is a maximum of 0.1, while the coefficient for plastic on sand is about 0.2-0.3.
We will acquire our test data through observation, assessment, an angle finder, and a scale. The angle finder will be used to record the ski and spindle angles. The scale will be used for the weight of the assembly. The observations and assessments will be provided during the test ride portion of the test.
The testing evaluation schedule takes place from April 6th – May 18th. Check APPENDIX E for the Gannt chart/schedule.
There are a number of resources that will be needed to proceed with the testing portion of
the project. The test bike is the main resource needed. The bike is a 2005 Honda CR250r, which should be equipped with a paddle (sand) tire and in running condition. Another resource requires that if snow is not testable, then sand should be used. A transportation resource is needed as well to transport the test bike to the various evaluation sites.
The data will be recorded in various ways depending on the tests being performed. An angle finder should be placed on the front ski while the test bike is on its stand; this test procedure will allow the front ski to rotate freely so that the maximum incline and decline angles can be found. The rest of the data will be acquired through observations and multiple assessments performed during the test ride. No computer programs will be required to process data, since pressures, temperatures, etc. won’t need to be recorded using a logger or equivalent machine. A number of the tests will be basic pass or fail recordings with a description of the performance outcomes.
Some operational limits are: the ski should not rotate past the maximum angle requirements in the incline/decline position, the spindle (column) should not rotate past its maximum constraint, and the assembly should not weigh more than its requirement. No operational limits are set for the test ride portion, but are rather set for the static functions of the SnowSki.
The precision of the testing will be maintained throughout all tests, since the ski will only achieve one set answer for the angle tests and similar results for the other procedures. The accuracy will be determined by the difficulty of each of the set goals/requirements. If the results aren’t close to the set requirements, then the accuracy will be low and will prove that the initial goals were set unrealistically.
The data shall be initially recorded/stored on a testing sheet and then transferred onto the official evaluation sheet located in APPENDIX G of this report. The data won’t need to be manipulated in excel or similar programs because no data points will need to be plotted.
The data will be presented in a table format.